Repair help
Why Is My GE Washing Machine Not Spinning?

AZparts Team
Updated on July 9, 2025
10 min read
When your GE washing machine does not spin, it can be incredibly frustrating, especially when you're left with soaking wet clothes. This common issue affects many GE washer owners and can stem from various mechanical problems or simple maintenance oversights. Understanding the root causes and knowing how to troubleshoot effectively can save you time and money. At AZParts, we specialize in providing genuine replacement parts for GE washing machines, helping you restore your appliance to optimal performance quickly and efficiently.
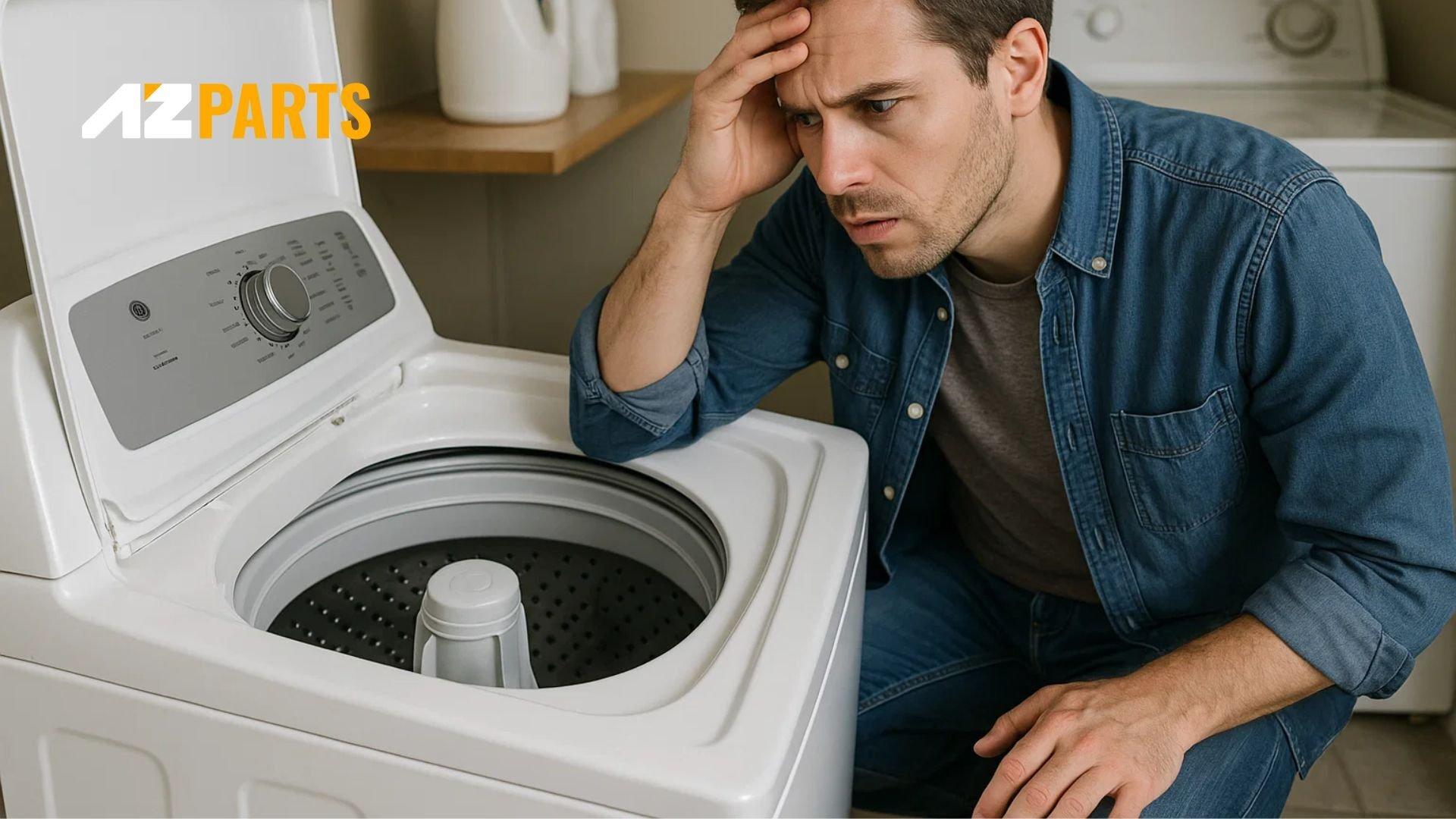
1. Common Causes & DIY Fixes
1.1 Unbalanced Load
When clothes bunch up on one side of the drum, the washer's safety mechanism prevents spinning to avoid damage. Heavy items like blankets or towels can easily create this imbalance, especially when mixed with lighter garments. The machine may attempt to redistribute the load by adding water or pausing the cycle, but severe imbalances will halt spinning entirely.
To fix this issue, stop the cycle and manually redistribute the clothes evenly around the drum. Separate heavy and light items into different loads when possible. For bulky items, add a few towels to help balance the load distribution. Always ensure you're not overloading the machine beyond its capacity specifications.
Unbalanced load washer make it not spin (Source: AZParts)
1.2 Faulty Lid Switch
The lid switch is a crucial safety component that prevents the GE washing machine from spinning when the lid is open. When this switch malfunctions, the washer believes the lid is open even when it's properly closed, causing the spin cycle to fail. Signs of a faulty lid switch include the washer filling with water but not agitating or spinning, or the cycle stopping mid-process.
You can test the lid switch by pressing it manually while the lid is closed. If you don't hear a distinct clicking sound, the switch likely needs replacement. A multimeter can also help verify electrical continuity. This is a relatively simple tips for fixing washer lid switch, which most homeowners can handle with basic tools.
1.3 Clogged or Kinked Drain Hose
A clogged or kinked drain hose prevents proper water drainage, which can interfere with the spin cycle. GE washing machines are designed to drain water before spinning, so any obstruction in the drainage system will halt this process. Common causes include lint buildup, small clothing items, or physical damage to the hose.
Inspect the drain hose for visible kinks or bends that might restrict water flow. Disconnect the hose and check for clogs by running water through it. Clean out any debris using a plumber's snake or high-pressure water. Ensure the hose is properly positioned and not crushed behind the machine.
Clogged or Kinked Drain Hose (Source: AZParts)
1.4 Worn Drive Belt
The drive belt connects the motor to the drum, enabling the spinning motion. Over time, this belt can stretch, crack, or slip off its pulleys, preventing the drum from spinning effectively. A worn drive belt often produces squealing noises during operation or may cause the drum to spin slowly or intermittently.
Accessing the drive belt typically requires removing the washer's back panel or cabinet. Inspect the belt for signs of wear, fraying, or stretching. A properly tensioned belt should have slight give when pressed but shouldn't be loose. Replace the belt if it shows significant wear or damage.
1.5 Broken Drain Pump
The drain pump removes water from the tub before the spin cycle begins. When this component fails, water remains in the drum, preventing proper spinning. A faulty drain pump may produce unusual noises, fail to drain water completely, or leak underneath the machine.
Test the drain pump by running a drain cycle and listening for motor sounds. If the pump runs but doesn't drain water, there may be a blockage. If it doesn't run at all, the pump motor likely needs replacement. This repair requires some technical skill and proper safety precautions.
Broken Drain Pump (Source: AZParts)
1.6 Drive Motor or Rotor Issues
The drive motor powers the entire washing process, while the rotor (in direct-drive models) helps control drum movement. Problems with either component can prevent spinning entirely. Motor issues often manifest as burning smells, unusual noises, or complete failure to start cycles.
Motor problems typically require professional diagnosis and repair due to their complexity. However, you can check for obvious signs like burnt wire connections or excessive vibration. Rotor issues may cause irregular spinning patterns or grinding noises during operation.
2. Let's Solve the Problem: How-to Troubleshoot
Step 1: Inspect the Lid Switch
Begin troubleshooting by examining the lid switch mechanism. Open and close the lid several times, listening for the distinctive clicking sound that indicates proper switch operation. Clean around the switch area to remove any dirt or debris that might interfere with proper contact. Use a flashlight to inspect the switch for physical damage or loose connections.
If the switch appears damaged or doesn't click properly, it needs replacement. This component is usually located under the main top or behind the control panel, depending on your GE model. Always disconnect power before attempting any repairs.
Inspect the Lid Switch (Source: AZParts)
>> Learn more: Washer Lid Won’t Lock? Causes & Troubleshooting Solutions
Step 2: Inspect the Drive Belt
Access the drive belt by removing the washer's rear panel or front cabinet, depending on your model. Examine the belt for cracks, fraying, stretching, or glazing. A healthy belt should be flexible but not loose, with no visible damage. Check that the belt is properly seated on all pulleys and hasn't slipped off.
If the belt appears stretched or damaged, measure its length and width to ensure you order the correct replacement. Note the belt's routing pattern before removal to ensure proper installation of the new belt.
Step 3: Inspect the Motor Coupling
The motor coupling connects the motor to the transmission in many GE washers. This component can wear out over time, especially with heavy use or unbalanced loads. A broken motor coupling will prevent the drum from spinning while allowing the motor to run.
Remove the cabinet to access the motor coupling, typically located between the motor and transmission. Look for broken or worn plastic pieces, which indicate coupling failure. This is a common wear item that's relatively inexpensive to replace.
Step 4: Inspect the Door Latch
For front-loading GE washers, the door latch mechanism must engage properly for the spin cycle to operate. Inspect the latch for damage, wear, or misalignment. Clean the latch area thoroughly, as soap residue or debris can prevent proper engagement.
Test the latch by closing the door and ensuring it clicks securely. If the door doesn't latch properly or the machine doesn't recognize a closed door, the latch assembly may need replacement or adjustment.
Inspect the Door Latch (Source: AZParts)
Step 5: Inspect the Motor Control Board
The motor control board regulates power delivery to the drive motor. Electronic failures in this component can prevent spinning while allowing other functions to work normally. Look for signs of burning, blown fuses, or damaged connections on the control board.
This component requires technical expertise to diagnose properly. If other mechanical components check out but the motor doesn't receive proper signals, the control board may be the culprit. Professional diagnosis is often recommended for control board issues.
Step 6: Inspect the Clutch
The clutch assembly allows the basket to gradually reach spinning speed. A worn clutch may produce excessive noise, fail to engage properly, or prevent the basket from reaching full spin speed. This component is subject to wear from normal use and may need periodic replacement.
Accessing the clutch requires significant disassembly of the washer. Listen for grinding or squealing noises during the spin cycle, which often indicate clutch problem with washing machine. This repair typically requires intermediate to advanced mechanical skills.
Step 7: Inspect the Rotor
In direct-drive GE washers, the rotor works with the stator to create the magnetic field that drives drum rotation. Inspect the rotor for damage, excessive wear, or loose magnets. A damaged rotor can cause irregular spinning or complete failure to spin.
The rotor is typically located at the bottom of the wash basket. Check for physical damage, corrosion, or debris that might interfere with proper operation. This component requires careful handling during inspection and replacement.
Inspect the Rotor (Source: AZParts)
Step 8: Inspect the Stator
The stator houses the electrical windings that create the magnetic field for drum rotation. Damaged windings or loose connections can prevent proper spinning operation. Test the stator windings for continuity using a multimeter to identify electrical failures.
Stator problems often require professional diagnosis due to the complexity of the electrical systems involved. However, visual inspection can reveal obvious damage like burnt windings or loose wire connections.
Step 9: Inspect the Drive Motor
The drive motor is the heart of the washing machine's operation. A failed motor will prevent all mechanical functions, including spinning. Check for signs of overheating, unusual noises, or failure to start when power is applied.
Motor testing requires electrical knowledge and proper safety procedures. If the motor doesn't respond to electrical input or shows signs of internal damage, replacement is typically necessary. This is often a job for qualified technicians.
3. Where to Buy Genuine GE Washer Parts
When your troubleshooting reveals the need for replacement parts, choosing genuine GE components ensures optimal performance and longevity. AZParts offers an extensive selection of authentic GE washing machine parts, from simple switches to complex motor assemblies. Our inventory includes:
- GE Washer Lid Switch Assembly - Direct replacement for faulty safety switches
- Drive Belt Kit - Complete belt and pulley system for reliable power transmission
- Motor Coupling Set - High-quality plastic coupling components for smooth operation
- Drain Pump Assembly - OEM pumps designed for your specific GE model
Where to Buy Genuine GE Washer Parts (Source: AZParts)
Each part comes with detailed compatibility information and installation guidance to ensure you get the right component for your specific GE washing machine model. Our technical support team can help identify the exact parts you need based on your serial number for washing machine and symptoms.
4. FAQs about GE washing machine does not spin
4.1. GE washer won't spin – is it worth repairing?
Whether to repair or replace your GE washer depends on the age of the machine and repair costs. For washers under 8 years old, most repairs are cost-effective, especially for common issues like lid switches or drive belts that cost under $100 to fix. However, if multiple major components fail simultaneously or the repair cost exceeds 50% of a new machine's price, replacement might be more economical.
4.2. Is there a reset button on the GE washing machine?
Most GE washing machines don't have a dedicated reset button, but you can reset the machine by unplugging it for 1-2 minutes, then plugging it back in. Some models have a "Control Lock" or "Delay Start" button combination that can clear error codes. Check your owner's manual for model-specific reset procedures, as methods vary between different GE washer series.
4.3. How do I balance a GE washing machine?
To balance your GE washing machine, first ensure it's level using the adjustable feet and a bubble level. Distribute clothes evenly around the drum before starting cycles, and avoid washing single heavy items alone. If the machine rocks during operation, adjust the leveling feet until all four corners are stable and the unit doesn't move during the spin cycle.
4.4. How to clean the drain pump filter?
GE front-load washers typically have a drain pump filter accessed through a small door at the bottom front of the machine. Place towels around the area, then slowly unscrew the filter counterclockwise. Clean debris from the filter and housing, then reinstall securely. Top-load models may not have accessible filters, but you can clean the drain system by running an empty cycle with a washing machine cleaner.
A GE washing machine that does not spin can often be repaired with proper diagnosis and the right replacement parts. By following these troubleshooting steps from AZParts systematically, you can identify the root cause and determine whether it's a DIY fix or requires professional service. Remember that safety should always be your first priority when working with electrical appliances.
For reliable, genuine GE washing machine parts and expert guidance, trust AZParts to help restore your appliance to peak performance. Visit our website today to find the exact components you need and get back to worry-free laundry days.
Contact Information:
- 8 The Green, Ste A, Dover, Delaware 19901-3618, United States
- support@azparts.com
Washer
Further Reading
Further Reading